The field that requires eddy current test is precision mechanical parts manufacturing, and it is the most suitable test technology for automated mass production test based on its high detection ability for micro cracks that occur after forging, processing, heat treatment, welding, and polishing.
The advantage of crack test using eddy current equipment is that it enables fast, reliable, and automated quality test of mass-produced precision mechanical parts without contact. It not only replaces magnetic part detection, but also provides a significantly higher level of detection compared to other non-destructive testing techniques.
The performance of eddy current equipment and sensors is critical to achieving fast and reliable automated test. To this end, EddyWorks developed its own software (learning function, etc.) and hardware that can maximize ease of use and test performance and applied it to test equipment.
The principle of test is that when the magnetic field generated by the eddy current sensor (coil) is transmitted to the metal close to it, an induced current is generated, which is called an eddy current.
Depending on the physical properties (chemical components) and the degree of structural change of the metal, the size and shape of the eddy current generated in the metal is detected differently, and the equipment detects it and can perform an automated mass production test.
Eddy current equipment can detect the cracks on the test products and perform automated mass production testing.
There are many different types of test products that can be tested such as shafts (bushings), drums, bearings, gears, bolts and washers.
EddyWorks’ equipment can be designed to mix up channels in one equipment with crack detection channels, structure test channels, tap detection channels and their any combinations. And it can simplify the system and lower investment costs.
Customized sensors are available for the special shape of the test object.
EddyWorks provides a sensor dedicated to the trajectory, allowing the entire trajectory to be inspected with just 1-2 scanning times. By using these dedicated sensors, equipment can be simplified and test C/T (Cycle time) can be dramatically shortened. This sensor is attracting attention from many bearing manufacturers at home and abroad.
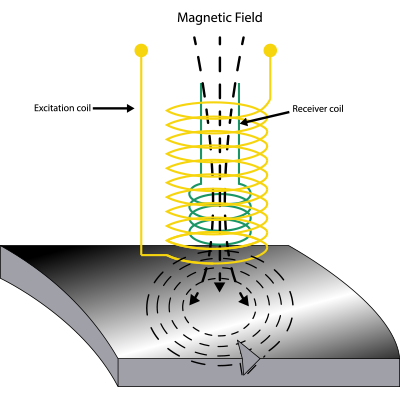
Examples of Crack tests
Shafts and bushings
샤프트 및 부싱류 크랙검사 예
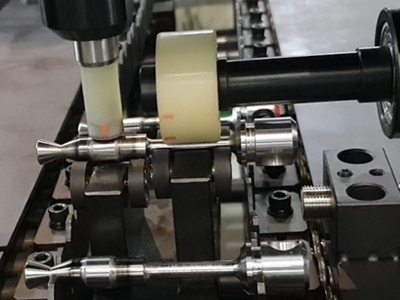
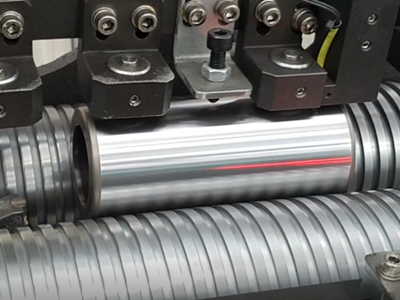
Bolts and washers
볼트 및 와셔류 크랙검사 예
Crack test of the bolt head and screw portion is possible, and microcrack test is possible using a sensor dedicated to the screw portion.
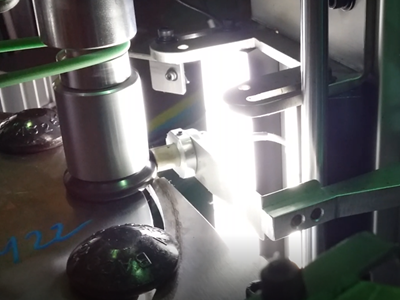
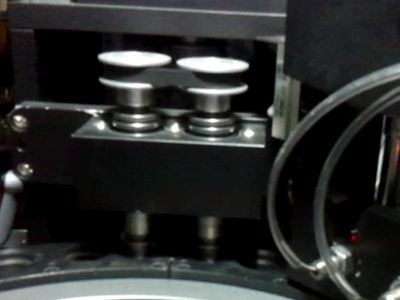
Gears, Splines
and Serrations
기어, 스플라인 및 세레이션 크랙검사 예
In order to detect microcracks in grooved areas such as gears and splines, special sensors and special functions of eddy current equipment are required, and high technical skills are required.
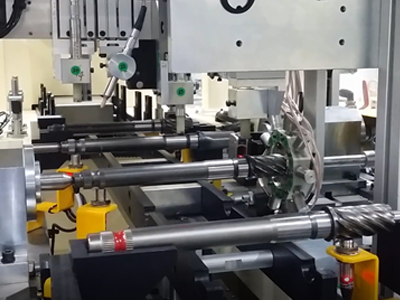
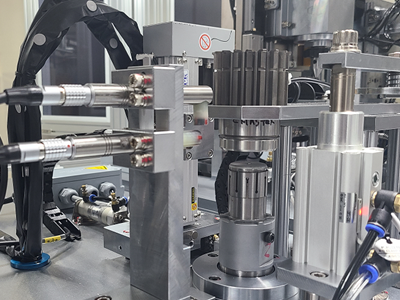
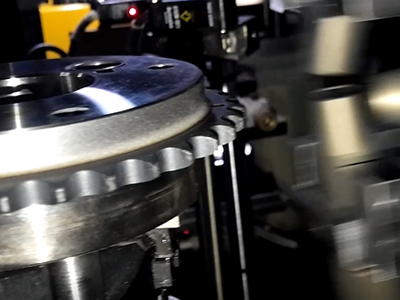
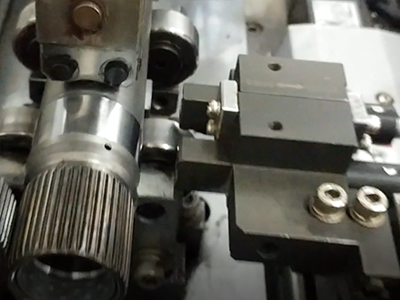
Bearings
Eddy works Co., Ltd. provides a sensor dedicated to the trajectory, allowing the entire trajectory to be test with just 1-2 scanning times. By using these dedicated sensors, equipment can be simplified and test C/T(Cycle time) can be dramatically shortened. This sensor is attracting attention from many bearing manufacturers at home and abroad
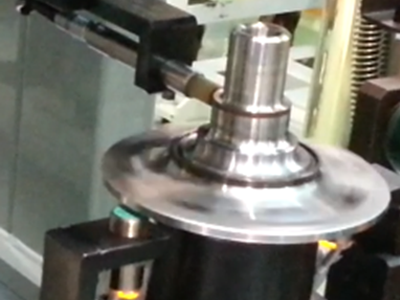
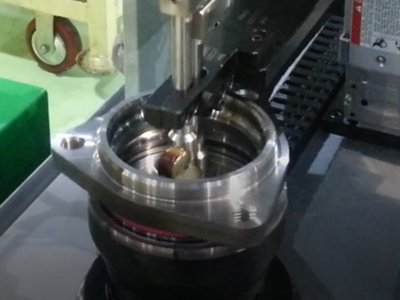
Crack test
of forged products
Mass production test for cracks occurring during hot forging and cold forging.
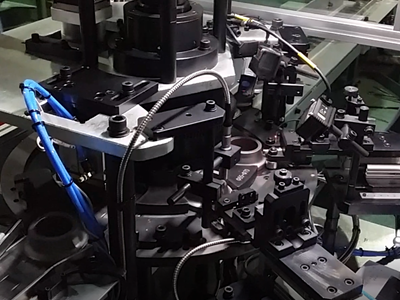
Test of defects after welding and drawing tubes (pipes)
튜브(파이프) 용접 및 인발 후 결함검사
Test of STEEL, SUS, aluminum tubes, and pipes for defects after welding and drawing.
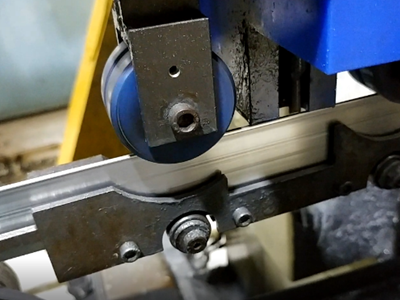
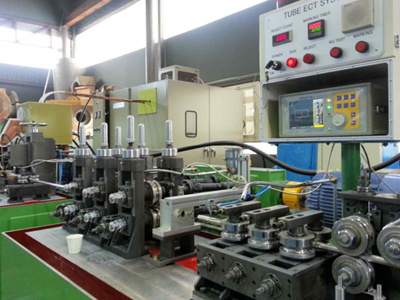
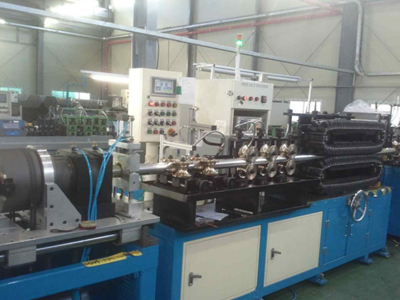
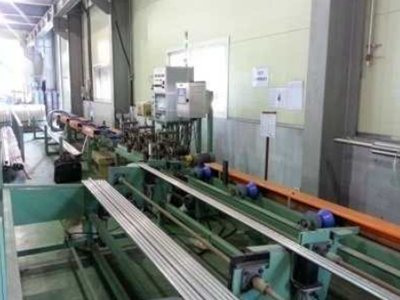
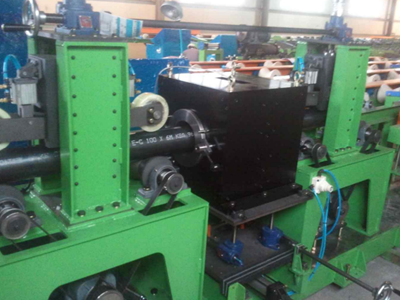