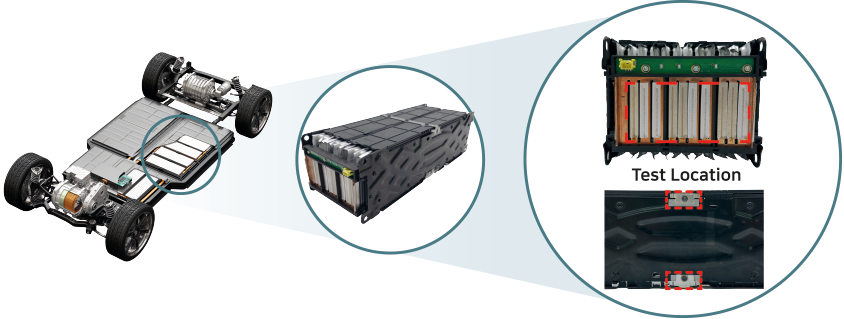
Battery welding test and eddy current test are technologies applied to testing and test of mechanical defects or material properties by generating an induced current in the test object due to the magnetic field created by the sensor.
All metals have conductor properties, and by generating induced current according to frequency, each impedance change (resistance component) can be obtained according to changes in the material or mechanical structure of the metal.
For example, when welding two base materials (CU-CU or AL-CU), the mechanical bonding structure of the normal welded part and the incomplete or unwelded part are different, which affects the change in impedance.
By generating eddy currents according to the type of welding, impedance changes can be obtained according to the mechanical bonding characteristics of the welding.
The eddy current generated in this way has a physical property of being created on the surface of the metal and penetrating to a certain depth within the metal. Therefore, the main variables of eddy current penetration are the metal material and the test frequency.
The figure below shows a graph of test frequency and eddy current penetration depth for each metal. The higher the test frequency, the more concentrated the eddy currents are on the surface. The higher the test frequency, the more concentrated the eddy currents are on the surface. The lower frequencies allow eddy currents to penetrate from the surface to specific parts of the deep, obtaining signals about changes in metal properties or mechanical structure and organizing automatic test.
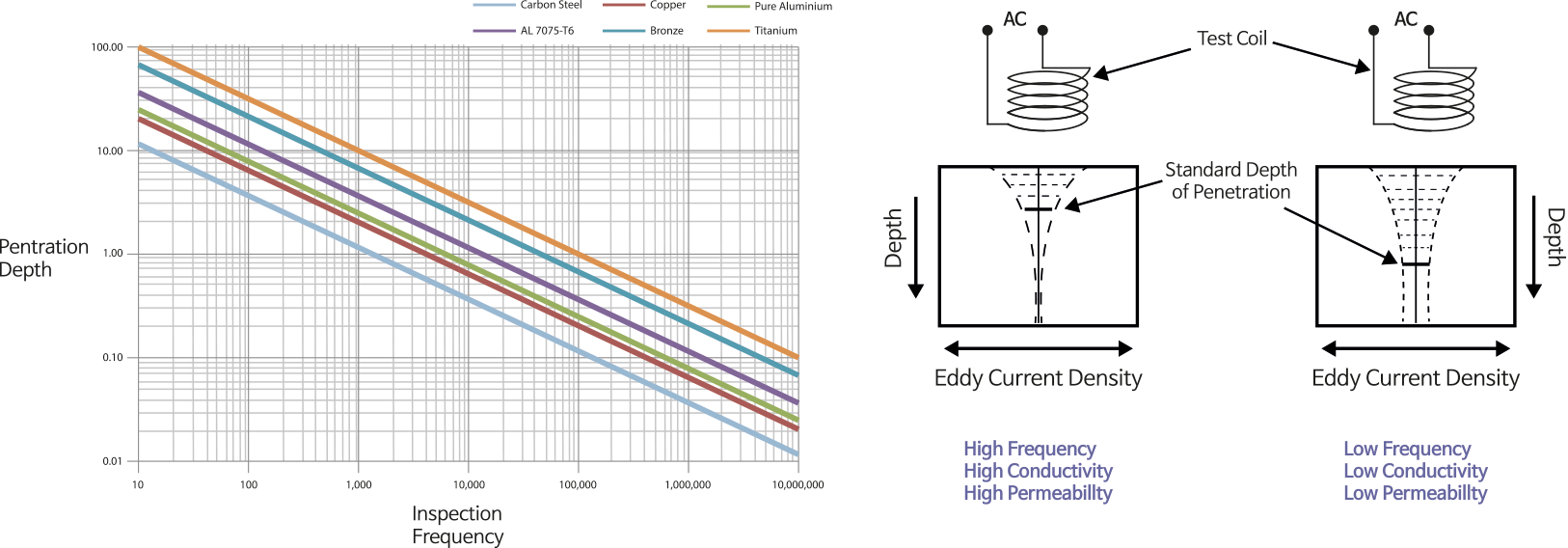
The test screen provides a cluster screen of test signals and a level meter screen, and the inspected data can be transmitted through communication.
During the battery pack manufacturing process, after welding the battery cell electrodes to the busbar, quality test of the welding condition is required to ensure the electrical safety of the battery.

Typical types of defects that can occur during welding are as follows.
After welding, the welding strength varies depending on the penetration depth, so differentiated test is required from the surface to the depth of the base material.
For the above reasons, MFT/MFET (Multi-Frequency ECT) technology allows test from the surface to the deep part of the test object using frequencies.
In summary, MFT/MFET technology can be a suitable test technology for battery pack electrode weld test.
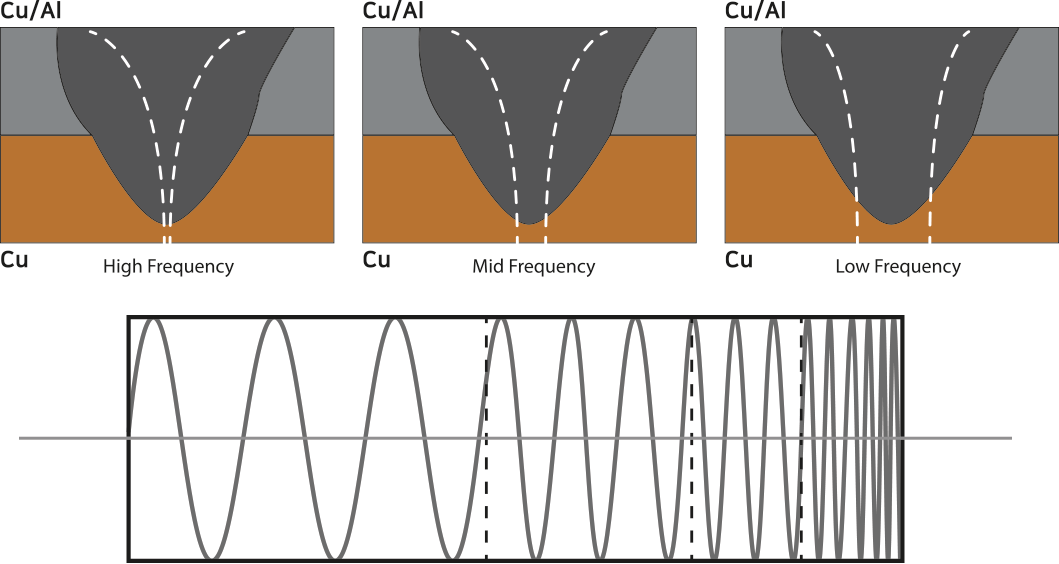
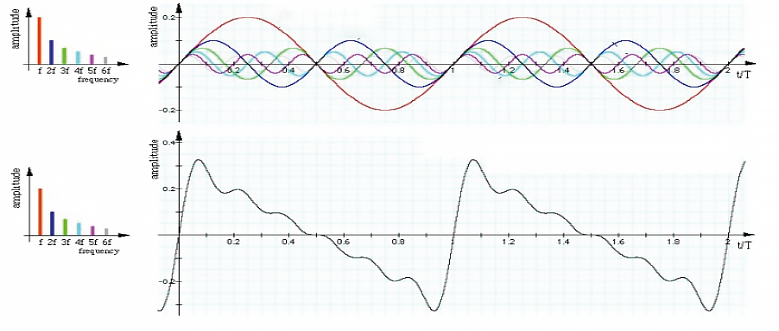